Creating attractive living
spaces
Safety, security and comfort
We are committed to constructing residences where residents can feel safe. As part of this commitment, we will pursue high quality and comfort and thoroughly implement measures against crime and natural disasters, such as earthquakes.
Quality Policy
Haseko Corporation's Quality Policy
Providing quality that meets customers' expectations
- The Company shall accurately grasp the social needs and changes, and provide buildings that are safe, secure, and comfortable.
- The Company shall endeavor to boost customer satisfaction through integrated sales, design, construction, and after-sales services.
- The Company shall pass on the technologies and traditions it has cultivated (the Haseko DNA) through personnel development and education.
- The Company shall work with its cooperating companies to enhance quality, striving to build better.
- The Company shall make ongoing improvements to its quality management system.
Quality management system
Framework to promote quality management system at Haseko Corporation

※Quality Management System
Background to obtaining ISO9001 certification
Haseko Corporation obtained ISO9001 quality management system certification in Tokyo and Kansai regions in March 1997 and July 1997, respectively. (In March 2018, we integrated quality management systems of the two regions.) To provide consistent quality, we apply this system to all divisions involved in quality management and enhance customer satisfaction. (Divisions for which certification has been applied as of April 1, 2024: the operating division , the Kansai operating division, the Tokai operating division, the urban development division, the Kansai urban development division, the construction divisions, the Kansai construction division, the design divisions, the Kansai design division)
Haseko Reform, Inc. obtained the certification in March 2014, and FUJIKENSETSU Co., Ltd. also obtained the certification in March 2000 for its Kansai Branch and November 2000 for its Tokyo Branch.
Going forward, we will continue to engage in quality management activities.
Initiatives and ongoing improvement
Upon conducting quality management activities, we formulate a quality policy, in
response to which each division sets quality goals and numerical targets and carries
out the activities accordingly. The quality management system is checked by internal
audit and external examination as to whether or not it complies with Haseko’s
determinations including specification requirements, and whether or not it is
implemented and maintained properly. Based on the results, the quality management
system is reviewed and improved on an ongoing basis.
The days on which external examination was conducted and the number of matters
pointed out in fiscal 2024 were as follows.
Date of registration/renewal | Date of external examination | Number of matters pointed out by the external examination |
|
---|---|---|---|
Haseko Corporation | Mar. 31, 1997 Mar. 31, 2024 |
Dec. 13-15, 2023 | None |
Haseko Reform, Inc. | Mar. 13, 2014 Apr. 19, 2024 |
Feb. 5-28, 2024 | None |
FUJIKENSETSU Co., Ltd., Tokyo Branch | Nov. 15, 2000 Nov. 15, 2021 |
Sep. 14, 2023 | None |
FUJIKENSETSU Co., Ltd., Kansai Branch | Mar. 1, 2000 Mar. 1, 2024 |
Nov. 29-30, 2023 | None |
Haseko Corporation’s quality education
As a company that provides safe and secure homes for our customers, we develop and implement an education and training curriculum each fiscal year for all personnel engaged in activities that affect quality, based on the ISO 9001 standard. We especially promote measures to encourage employees to obtain technical qualifications, such as first-class registered architect qualifications and first-class construction managing engineer qualifications, which include the acquisition of important knowledge for ensuring quality. We also train internal quality auditors from the construction, design, and technological promotion divisions, and strive to develop personnel capable of auditing from a customer standpoint and perspective.
Quality Management in the Supply Chain
Quality Education for Suppliers (Cooperating Companies)
Haseko Corporation, together with “Ken-ei-kai,” an organization of main cooperating companies, is engaged in value enhancement activities to provide high-quality condominiums. As part of these efforts, our “construction quality improvement division” also helps cooperating companies provide quality education.
Specifically, the Tokyo construction quality improvement division holds annual “expanded workshops” for employees of all cooperating companies working on our construction sites, in addition to corporate members of “Ken-ei-kai.” At the workshops, we explain the issues indicated and points to be noted from previous completion inspections, as well as issues to be kept in mind during construction works, to the various subcommittees: the Building Frame Subcommittee, the Facilities Subcommittee, the External Structures Subcommittee, the Interior Works Subcommittee, and the Exterior Works Subcommittee. After the workshops, we accept questions, suggestions, and requests. Considering and replying to them provides opportunities for improvement. In addition, “Ken-ei-kai” members carry out monthly on-site patrols to check the thorough implementation of points to be noted and provide guidance, as well as to hear feedback from workers on-site and identify issues requiring consideration (The session in fiscal 2023 was attended by 1,497 people.).
A “Debriefing Session on Value Enhancement Activities” is also held once a year to spread knowledge of the status and results of all value enhancement activities. Timely themes are selected for the sessions, and they introduce the employees of all cooperating companies and construction workers working on our construction sites to the content of value enhancement activities undertaken over the past year. (The session in fiscal 2023 was attended by 4,404 people.)
We are undertaking similar initiatives in Kansai and Tokai regions as well.
Continuous Evaluation of Suppliers (Cooperating Companies)
We engage in the continuing assessment of cooperating companies to accurately grasp their capabilities and facilitate guidance and education. Specifically, we assess all primary cooperating companies* at each construction site regarding aspects such as quality management, safety and health management, environmental management, process management, and cost management, on the completion of each construction. In cases where we consider improvement necessary, we request them to make improvements while implementing education as required.
In addition, in order to fulfill its social responsibility across the entire supply chain, the Haseko Group requests its business partners to comply with the Haseko Group Sustainable Procurement Guidelines, which include matters regarding securing quality, obtains written consent from its main business partners, and regularly verifies their compliance through questionnaires using a self-checklist.
*Primary cooperating companies: Cooperating companies with a direct contractual relationship with Haseko Corporation.
Audit of supplier's factories
For materials related to the structure, etc., especially those that assumed to have quality risks, of buildings, we work to ensure quality by auditing suppliers' factories, in addition to conducting receiving inspections at construction sites and other measures. In the audits, HASEKO Corporation technical division employees check the factories' quality control system and their actual operations, according to the checklist. We implement these factory audits when considering the adoption of new materials from such factories, and on a regular basis according to the risks by material type.
The factories to be audited include those of upstream suppliers, not limited to those of suppliers contracted directly by HASEKO Corporation, as distribution channels vary depending on the type of material.
Quality maintenance and improvement
Haseko Corporation has accumulated tremendous know-how concerning how to construct condominiums to heighten customer satisfaction from its experience of building over 700,000 condominium units. We have collected know-how to create unique quality assurance standards and apply these standards to all condominiums we design and construct. (Our unique quality assurance standards include “design guidelines,” which form our standards for design, and “standard plans,” which summarize detailed construction methods. The standards are shared among our technical divisions.)
We continue to hold meetings across the Architecture & Engineering, Construction, and Technological Promotion Divisions to share “real feedback from condominium residents,” “information from condominium refurbishment & maintenance management companies,” and “construction information from construction sites” gathered by Haseko Corporation and Group companies. Any matters requiring action are communicated to departments through the relevant meeting body, standards are added, revised, or improved, and periodically reflected and disseminated through the “design guidelines” and “standard plans,” to continually improve quality.
Construction of “resilient” condominiums considering the prevention and reduction of disaster
Damage caused by natural disasters and earthquakes is becoming increasingly serious. In order to provide homes that are even more "safe, secure, and comfortable," we have taken advantage of the collective strengths of the Haseko Group to implement disaster countermeasures in both hardware and software, creating disaster-resistant condominiums that can recover on their own even if a disaster occurs. We are promoting the creation of disaster-resistant condominiums that can recover on their own even if a disaster occurs.
Providing services under the Proposal of Hazard-resistant Condominium
In 2018, many residential homes were significantly affected by natural disasters
including the Earthquake in Northern Osaka Prefecture and Typhoon Jebi (No. 21)
which crossed the Kinki region. The Disaster Resilient Technology Working Group,
which was established by the Haseko Group in the wake of increasingly severe natural
disasters, has prepared and has been providing services based on the Proposal of
Hazard-resistant Condominium covering exclusive and communal areas, essential
services, as well as operation and management.
The Proposal will be actively made to properties inside and outside the Group for
adoption to support residents both from the tangible and intangible aspects of the
Haseko Group’s safe, secure and comfortable condominiums leveraging the advantages
of collective living.

Development and introduction of the Smart Water Tank that utilizes rainwater efficiently
Haseko Corporation and Haseko Property Management Holdings Inc. have developed the Smart Water Tank as a disaster prevention and environmentally-friendly initiative and pushed forward with the adoption of the product to the Group’s for-sale condominiums. This facility stores rainwater taken from the condominium roof and makes efficient use of the stored rainwater for watering plants during normal times to help preserve water resources, and in emergency situations, it can supply drinking water to residents for six days (three liters per person per day) by using the WELLUP emergency water purification system. In the future, we plan to install the Smart Water Tank as a standard specification for projects of over 200 units designed and built by Haseko Corporation.

Installation of partitions with enhanced resistance to strong winds
(partition boards between units)
In an environment of increasingly severe disasters brought about by global warming and worsening levels of damage caused by strong winds in major typhoons, highly resilient outdoor partitions are a necessity. Since 2020, Haseko Corporation has made its “SH Partition”* (designed with high wind resistance to withstand a once-a-century major typhoon) part of its standard specifications. In December 2023, with a view to improving the design of the “SH Partition,” we developed a new “SH Glass.”
We will continue to propose and adopt these products in projects, and work to create safe, secure, and comfortable housing.
*SH Partition: “SH” is an abbreviation of Super High
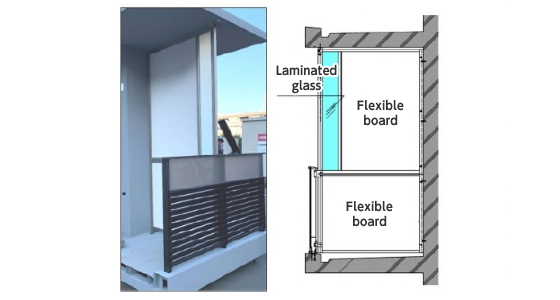
Haseko's "Three-piece set disaster prevention equipment" to secure post-disaster living necessities
The Haseko Group has long believed that it is important to not only ensure the basic performance of condominiums per se, but also develop the framework to secure the basic necessities of life for residents after a disaster has occurred. From such perspective, we became the first in Japan to adopt an emergency potable water generation system in a for-sale condominium in 2003, and have since been putting efforts into adopting and proposing the “three-piece set disaster prevention equipment”—which consists of an “emergency potable water generation system,” “emergency manhole toilets,” and “benches that convert into cooking stoves” as disaster prevention equipment to secure post-disaster living foundation, i.e., water, toilets and fire—in for-sale condominiums designed and constructed by us.

prevention equipment
Hosoda Corporation - Proposal of disaster prevention equipment set
Disasters can happen at any time. It is very important to be prepared on a daily
basis.
Hosoda Corporation proposes the adoption of a five-piece disaster prevention
equipment set to support the securing of lifelines in the event of an emergency in
for-sale new detached houses and to customers who are remodeling their own houses.
- Enjyu Branch
(For new construction/steel damper vibration control walls) - Steel damper vibration control walls are a standard feature of Hosoda Corporation’s Hybrid Cube construction method. It absorbs building sway and minimizes damage to a house.
- Eslon drinking water storage system
- The system can store 36 liters of fresh water, three days’ supply for a family of four (three liters per person per day). The underfloor plumbing space can be effectively utilized to ensure the largest living space.
- Home dam RWT-110
(Rainwater utilization tank) - Rainwater, a blessing of nature, can be stored and used for watering gardens and flowerbeds, and stored rainwater can also be used as water for daily life in the event of a water outage in an emergency.
- Earthquake-sensitive breakers
(Residential distribution board with earthquake-sensitive function) - Automatically shuts off electricity when an earthquake of seismic intensity of upper 5 or higher is detected. This is useful for preventing electrical fires when power is restored.
- Detachable footlight
(Home security light with brightness sensor) - Usually used as a night light, it automatically turns on as a security light during a power outage and can be detached from a wall outlet to be used as a portable electric light in an emergency.
Creation of New Values by Means of Condominium Renewals
It is said there are approximately 1,030,000 aged condominiums constructed under the former earthquake resistance standards (those of 1981 or before). Lack of aseismic capacity, aging buildings and facilities, aging residents as well as the question of how to renew condominiums have become social issues. The Haseko Group has established a framework to provide one-stop support for a variety of phases (including grasping of actual conditions through the evaluation of aseismic capacity, building diagnosis, and/or equipment diagnosis, deliberation of policies for rebuilding or life elongation considering the results of said evaluation and/or diagnosis, building of consensus between residents, design, and construction work) to cope with condominium renewals. The Group will create new values by coping with condominium renewals, making the most of its experiences in condominium construction, thereby contributing to the resolution of social issues.
- The total number of condominiums repaired/renovated: 840,000
(Renovation work of over 10.00 million yen in and after 2000; as of the end of March 2024) - The total number of condominium buildings rebuilt: 46
(As of the end of March 2024; completed constructions)
Haseko Group's rebuilding history
(Examples of rebuilding works completed since fiscal 2012)
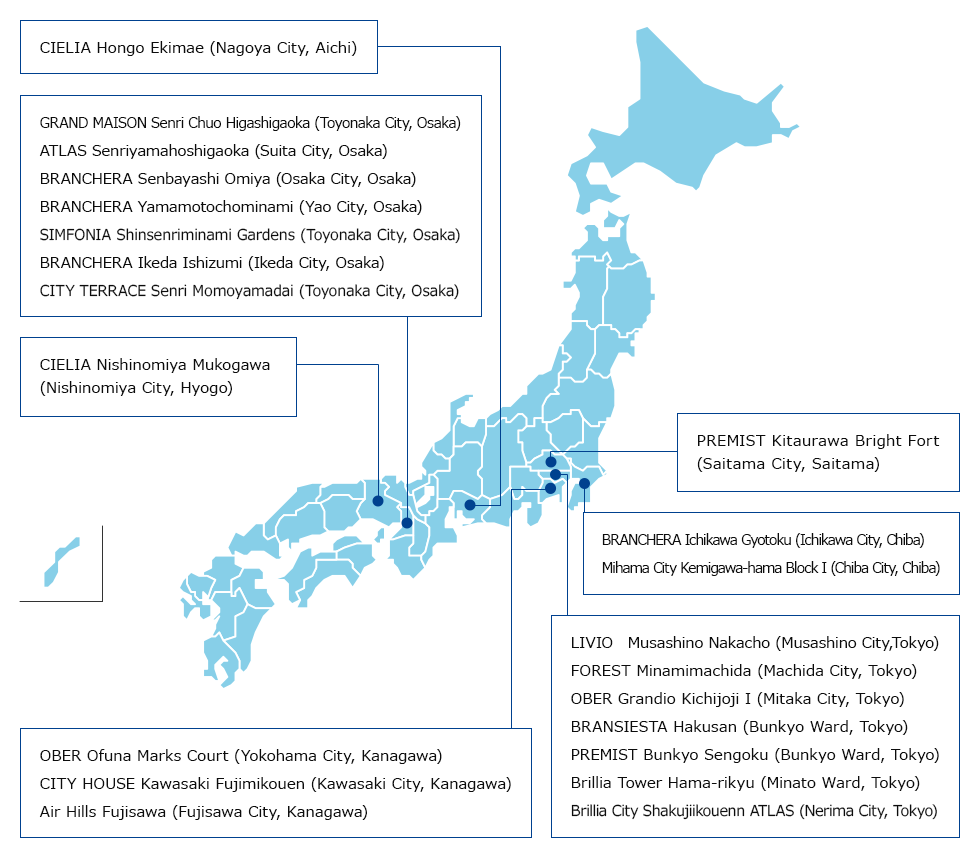
Example of rebuilding work: Wakashio Heights Reconstruction project “Mihama City Kemigawahama”
In 1973, Chiba hosted its first National Sports Festival, the “Wakashio National Sports Festival,” and for the first time, an athletes’ village was established for the National Sports Festival. The athletes’ village was sold after the Festival, which were held from summer to fall, and became “Wakashio Heights.”
When the buildings were completed in 1973, they were occupied mainly by young families, but after 30 years, they were facing various issues such as a deteriorated water supply and drainage pipes and the inconvenience of not having an elevator.
In 2008, Haseko Corporation joined the project as a consultant and began studying its rehabilitation. After a period of approximately five years, a rebuilding policy was determined in 2013, and a rebuilding promotion committee was established. A scheme was established to provide temporary housing within the complex during the construction period, which is inevitable in the reconstruction of condominiums.
The rebuilding promotion committee also actively engaged in consensus formation, reaching out to the community within the complex, and a resolution to rebuild the entire building was passed in December 2016. Block I (397 units in total) was completed in December 2020 and transformed into a next-generation condominium with EV and PHEV vehicle charging facilities installed in 45% of the parking spaces.
Construction of Block II (612 units in total) is steadily progressing toward completion in 2025. Haseko Corporation is participating in this project as a consultant, participating partner, and designer/builder.


Example of longer service life: Seismic reinforcement of
condominiums currently housing residents
Development of Haseko Non-brace Reinforcement Frame Method
Existing condominiums with concerns over anti-seismic performance often have
difficulty in obtaining seismic diagnosis and reinforcement work due to reasons such
as “no budget for reinforcement work,” “no budget for diagnosis fees,” “lack of
interest in seismic diagnosis,” and “lack of interest due to increasingly aging
residents” (source: “Survey Results of Current Condition of Condominiums,” by the
Bureau of Urban Development, Tokyo Metropolitan Government, March 2013). In addition to the Haseko Group’s existing earthquake resistance initiatives, such as aseismic capacity evaluation, repair and design, and construction work, we continue to develop technology that allows condominium residents to continue to live in their units while the units are being refurbished with aseismic features. One such technology we have developed is the unique, aseismic reinforcement “Haseko Non-brace Reinforcement Frame Method,” a construction method that does not compromise the view from condominium units and allows residents to continue to reside in them while construction takes place.
This seismic reinforcing method does not use diagonal braces that may obstruct the
view but instead uses reinforcing puncheons, which allows reinforcing effects to be
adjusted. Also, installing reinforcing frames consisting of wide flat beams,
reinforcement columns, and reinforcing puncheons increases seismic capacity.
Furthermore, although conditions apply, the reinforcement frames can be installed in
middle floors, foregoing ground installations of newly installed frames as required
in existing methods.
In the future, we will make the Haseko Non-brace Reinforcement Frame Method widely
known as an option for existing condominiums which need to be reinforced for
earthquake resistance and proactively make proposals combining other seismic
reinforcement methods that are optimal for individual situations and requests.
Benefits of the Haseko Non-brace Reinforcement Frame Method
- The view from the balcony is less compromised
- Work is possible while residents continue to live there as in-unit work is not required
- Lower cost than other existing reinforcement methods
- Environmentally-friendly method as demolition and removal of existing buildings are kept to a minimum

(Wide flat beams (yellow), reinforcement columns (green), reinforcing puncheons (blue))

Renovation example: Sustaina Branche Hongyotoku
Completed in September 2023, “Sustaina Branche Hongyotoku” is Japan’s first rental condominium project that achieves virtually zero CO2 emissions during building operation by completely renovating existing corporate housing with the aim of further promoting research and technological development to create new housing value.
This condominium introduces various state-of-the-art technologies of the Haseko Group, including energy-saving technologies that contribute to realizing a decarbonized society, technologies for extending the life of buildings, and wellness housing technologies. In order to create future housing that makes maximum use of IoT devices and AI technology, 13 out of 36 units are designed as experimental residential housing where environmental data are collected for developing new technologies.
This project was selected for the “Next Generation Housing Project 2022” which contributes to public awareness of leading technologies, as a “residential-type experimental home for creating future housing with smart home systems,” in the “Leading Businesses of Sustainable Buildings etc. (Next-Generation Housing) program in FY2022 2nd” conducted by the Ministry of Land, Infrastructure, Transport and Tourism.


- Related information
New utilization of existing condominiums
Haseko Reform Inc. works on a variety of renovation businesses, exploring new ways to utilize existing condominiums.
We carry out “renovation of whole condominium complexes,” implementing diagnosis, repair, renewal, and renovation of whole condominium complexes as total, “facility and shop renovation (e.g.: BRANCHEILE Igusa)”, implementing renovation of facilities such as elderly housing, etc. and stores, and complete renovation of corporate housing apartments for providing sustainable housing.
In addition, Haseko Reform Inc. continuously exhibit at the annual “Reform & Renewal Show” held in every May and widely discloses its corporate activities to the public.


- Related information
"Haseko's Premium After-sales Service"
After-sales service for perpetual and comfortable residency

Haseko Corporation has treated after-sales service as an important quality of condominiums. In 2008, we thus introduced Haseko’s Premium After-sales Service (PAS) to get a grasp of the status of condominiums more accurately and take optimal action in a speedy manner by listening to our customers’ opinions directly. To date, this service has been provided for 122,973 units. A total of 15,190 cases were handled in fiscal 2023, with 12,221 from the Tokyo region and 2,969 from the Kansai region.
Back in the day, the common procedure was to receive a call via a condominium management company. With the introduction of PAS, customers' opinions are communicated directly to Haseko (i.e., the builder), allowing first-class registered architects and other staff with expert knowledge of condominiums to respond and thereby facilitate technicians' actions.
PAS not only serves as a call center, but also provides support from all angles so that the home can be used for a longer period of time, including the extension of the after-sales service period, the enhancement of periodic services, and the distribution of "Maintenance Handbook for Housing" and "Tool Kit for Maintenance." Furthermore, comments received at the call center and results of periodic inspections by the inspection team are shared at feedback meetings attended by the design, construction, and technological promotion divisions as well as the management companies. They are also reflected in properties undergoing design and construction. We hope to contribute to the safe and secure living of residents by adopting PAS in more properties in the future.



After-sales service by Hosoda Corporation
Hosoda Corporation, which has strived to provide safe, secure, and comfortable housing for many years, provides a guarantee of up to 60 years under its built-to-order free plan.
The initial guarantee period for foundations, structural framework, and waterproofing is 30 years. This period may be extended for a further 10 years pursuant to an inspection and paid maintenance works carried out in the 30th year. Thereafter, the guarantee period may be further extended to a maximum of 60 years (in combination with the initial guarantee period) by performing inspections and paid maintenance works every 10 years for foundations, structural framework, and waterproofing, and every 5 years for pest prevention.
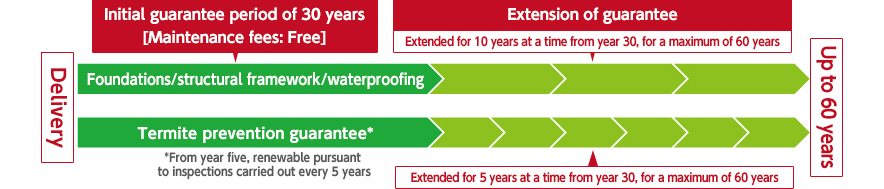
Haseko Community Owl 24 Center:
Defending home safety and security around the clock, 365 days a year
Haseko Community Owl 24 Center, a comprehensive monitoring center owned by Haseko Community, Inc., monitors alarms of condominiums 24 hours a day, 365 days a year. In the event of an emergency situation, the Center will receive an automatically-forwarded alarm or a telephone call from a resident, promptly get a grasp of the situation and dispatch security staff. The Center also serves as an out- of-hours point of contact by telephone.

- Related information
- Sustainability TOP
- Message from the Management
- Message from the Officer in Charge of Sustainability Promotion
- Haseko Group's Sustainability Management
- Climate Change Response
- The Digital Transformation Strategy of the Haseko Group
- D&I at the Haseko Group
- Creating attractive living spaces
- Building a company worth working at
- Protecting the precious environment
- Nurturing a culture of trust
- ESG Data and Disclosures
- External Evaluations and Awards
- Integrated Report
- Philosophy and Policies
- Special feature archives